Perfil de tornillos
Screw profile
El proceso de obtención de longitudes ilimitadas con una sección transversal constante, conformando el material al obligarlo a pasar a través de una boquilla bajo condiciones controladas de temperatura y presión, la extrusión de los compound preferentemente se lleva a cabo en una extrusora de tornillos gemelos. En el proceso de extrusión la materia prima viene en varias formas como pellets sólidos y cortos cilindros que vienen de un proceso anterior conocido como peletizado el cual permite el fácil acceso del material desde la tolva al husillo.
Husillo o tornillo
La principal función de la sección de alimentación de un tornillo es transportar sólidos. En base al comportamiento del flujo de los polímeros, el husillo o tornillo ha evolucionado ampliamente con en el mundo del copound y es la parte que contiene la mayor tecnología dentro de una máquina de extrusión, por lo tanto es la pieza que en alto grado determina el éxito de una operación de extrusión. Cuando se comienza la construcción de una máquina extrusora, debe identificarse el tipo de material a procesar para poder hacer un diseño óptimo del tornillo extrusor.
Principales tipos
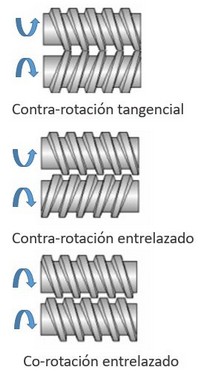
Los principales tipos de equipos para el procesamiento de materiales poliméricos a través del método de extrusión incluyen extrusoras de un solo husillo, doble husillo, pistón y disco. La parte más importante en un extrusor es el tornillo ya que es la parte que mezclará, fundirá y transformará el plástico fundido, La configuración de los tornillos interiores son una fuerza motriz dependiente del tipo de polímero o elastómero. Los tornillos constan de álabes, éstos son las roscas del tornillo que impulsan el material a través del extrusor. Se puede aplicar en una gran variedad de formas. Se pueden dividir en dos tipos, simple o doble tornillo, el simple tornillo se usan para la producción de tubería PVC, TPU y la extrusora de doble tornillo o de tornillos gemelos, la cual presenta una mejora en la mezcla y en el transporte del polímero. Se está llevando a cabo un número creciente de tareas de composición en extrusoras de doble tornillo, debido a su funcionamiento continuo, versatilidad y acción de mezcla efectiva. Estas máquinas ofrecen varias ventajas sobre las extrusoras de un solo tornillo. Una mejor alimentación y características de transporte más positivas permiten que la máquina procese materiales difíciles de alimentar, como polvos, materiales resbaladizos, etc. y produzca tiempos de residencia cortos y un espectro de distribución de tiempo estrecho. Una mejor mezcla resultante de un alto aporte de cizallamiento y áreas de transferencia de calor más grandes permiten un buen control de las temperaturas del stock. Un buen control sobre los tiempos de residencia y las temperaturas de las existencias obviamente son elementos clave en el perfil. Existen varios tipos de extrusoras de doble tornillo disponibles comercialmente. Difieren en su diseño y principios operativos, por lo tanto, en sus habilidades para la mezcla distributiva y dispersiva y, por lo tanto, en sus áreas de aplicación. Las extrusoras de doble husillo disponibles se pueden clasificar como co-giratorias y contrarrotativas, en función de la dirección de rotación de los tornillos. Las extrusoras contrarrotativas pueden clasificarse nuevamente en términos del grado de entremezclado de los tornillos, que van desde completamente entremezclados, donde el vuelo de un tornillo encaja firmemente en el canal del otro tornillo, hasta "tangencial" no entrelazado, donde Los dos tornillos giran libremente en sus barriles. Las extrusoras de doble husillo co-giratorio no se producen en el modo sin entremezclado. Se pueden encontrar más diferencias en forma de vuelo de tornillo. Los diseños de co-rotación, por ejemplo, pueden tener vuelos de tornillo redondeados o denominados autolimpiantes, que tienen grandes holguras de canal a través de la zona de entremezcla, o canales y vuelos de forma trapezoidal con flujo entre canales más restringido. Esto puede tener implicaciones importantes con respecto a su eficiencia de transporte positiva y la naturaleza de la mezcla entre los tornillos. Los tornillos con forma trapezoidal son generalmente más efectivos en ambos aspectos. Las extrusoras de doble husillo co-giratorio se producen comúnmente en el modo totalmente entremezclado y funcionan según el principio del bloque de construcción (modular). El barril se puede ensamblar en secciones, con cada sección calentada y enfriada individualmente. Los elementos de tornillo se seleccionan y ensamblan en dos ejes de tornillo con llave para cumplir con los requisitos de la tarea de mezcla. Los elementos comúnmente empleados incluyen elementos voladores regulares diestros y zurdos (hacia adelante y hacia atrás), discos de amasado hacia adelante y hacia atrás, y pasadores de mezcla y cizallamiento. Los diseños de elementos también vienen con varias formas y dimensiones. Los elementos de rotación transportan el material de alimentación hacia la cuña inferior donde el material es comprimido y transportado por el otro tornillo. El material continúa moviéndose aguas abajo de un tornillo al otro en un patrón de figura. Muy poco material pasa a través del espacio libre entre los tornillos que rotan en direcciones opuestas en el área de intermesh. Por lo tanto, prácticamente todo el material se transfiere de un tornillo al otro en cada revolución, lo que resulta en una renovación
completa de las superficies. Los efectos de mezcla y amasado en la extrusora pueden alterarse organizando y seleccionando discos. Estos discos, dispuestos en una configuración escalonada, proporcionan una mezcla transversal intensiva por fuerzas de corte de intensidad variable. Dependiendo del ángulo escalonado, se pueden generar secciones de tornillo neutro, delantero o inverso. En el modo neutro, el material se transfiere de la mitad del barril a la otra mitad en forma de figura ocho antes de ser presionado para avanzar en la dirección axial por los siguientes elementos fundidos. La acción de calandrado (es decir, paso del material a través del la separación de alta velocidad de corte entre los dos discos) genera una excelente mezcla dispersiva. La introducción de elementos inversos generará una mezcla más extensa en la dirección axial. Debido a la flexibilidad de diseño y la acción de mezcla efectiva, las extrusoras de doble husillo co-rotativas se usan ampliamente en la actualidad para una multitud de aplicaciones, incluida la incorporación de rellenos y refuerzos a plásticos, concentrados aditivos, mezclas de polímeros, formulaciones de PVC y extrusión de reacción.
Diámetro
El diámetro es la dimensión que influye en la capacidad de producción de la máquina y generalmente crece en proporción con la longitud del equipo. A diámetros mayores, la capacidad en kg/hr es usualmente superior, pero tiene una velocidad de rotacion del tornillo mas baja. Al incrementar esta dimensión debe hacerlo también la longitud de husillo (relación L/D) , ya que el aumento de la productividad debe ser apoyada por una mejor capacidad de plastificación.
Relación L/D
Relación L/D La definición del factor L/D (relación entre longitud de la hélice o tornillo y diámetro del tornillo). La longitud de la hélice se mide desde el lado frontal del puerto de alimentación hasta el final del tornillo, algunos miden la longitud de la hélice desde el centro del puerto de alimentación. La importancia que tienen la longitud y el diámetro del equipo (L/D), determina muchas propriedades final del compound, por lo tanto se acostumbra especificar las dimensiones principales del husillo como una relación longitud/diámetro (L/D). La selección del tamaño del extrusor y la combinación de la unidad, la L/D debe evaluarse cuidadosamente. En el pasado las extrusoras generalmente tenían un diámetro de 130 - 150 mm con una relación longitud / diámetro (L/D) de 20:1 y 24:1 y se consideraba larga. En los ultimos anos las extrusoras se han vuelto más largas y las relaciones desde 30:1 hasta 36:1 con un diámetro de 50 - 90 mm. Algunas extrusoras incluso superan relaciones de 40: 1 para fines especiales, como compounding o procesamiento a alta velocidad.
Qué beneficios proporciona una mayor longitud ?
Principalmente proprorciona una mejor calidad del material, gracias a una homogeneización mejorada y una mayor producción. Dado que la sección de alimentación mantiene aproximadamente la misma longitud, independiente de la relación L/D, el resto del tornillo se dedica a la fusión y bombeo. Cuanto mayor sea la capacidad específica, osea más profundos son los canales del tornillo, se necesitará una mayor longitud para completar la fusión y desarrollar la presión necesaria para empujar el polímero a través del dado. Por supesto, existe un límites real para aumentar la productividad a medida que aumenta la relación L/D. Por lo general, estos límites se deben a la incapacidad de la sección de alimentación para entregar más polímero. En los tornillos de menor diámetro, esto límite está determinado por la resistencia del tornillo, porque en los tornillos pequeños, solo se se puede profundizar poco los canales de tornillo per un limite fisico del tornilo mismo, mientras en la extrusoras grandes, la eficiencia de la alimentación disminuye a medida que los canales se hacen más profundos. Pero algunos polímeros, con extrusoras más largas se derriten mucho más fácil y más rápido que otros.
Sección de alimentación del tornillo
La configuración geométrica del tornillo, depende fundamentalmente del material a transformar, sin carga, con fibra de vidrio etc. por lo tanto es necesario tener en cuenta cada una de las variables que componen el tornillo. Los tornillo son componible con difrentes elementos como la sección de alimentación es el primer elemento del tornillo al que se le introduce polímero. Típicamente, en extrusores de agujero liso, ésta es la parte más profunda del tornillo y su función es transportar los sólidos.
El llugar donde la mayor parte de la fusión del polímero sucede en la sección de compresión o transición. Esta es la porción del tornillo que trasciende desde la profundidad de alimentación hasta la profundidad de dosificación, y es donde se efectúa trabajo sobre la resina, haciendo que se produzca la fusión. La raíz es gradualmente menos profunda, forzando al material hacia delante de la pared del barril, donde la fusión se lleva a cabo.
La sección de bombeo en el tornillo es donde se completa la fusión del polímero, y donde se genera presión para superar la restricción impuesta por el cabezal.